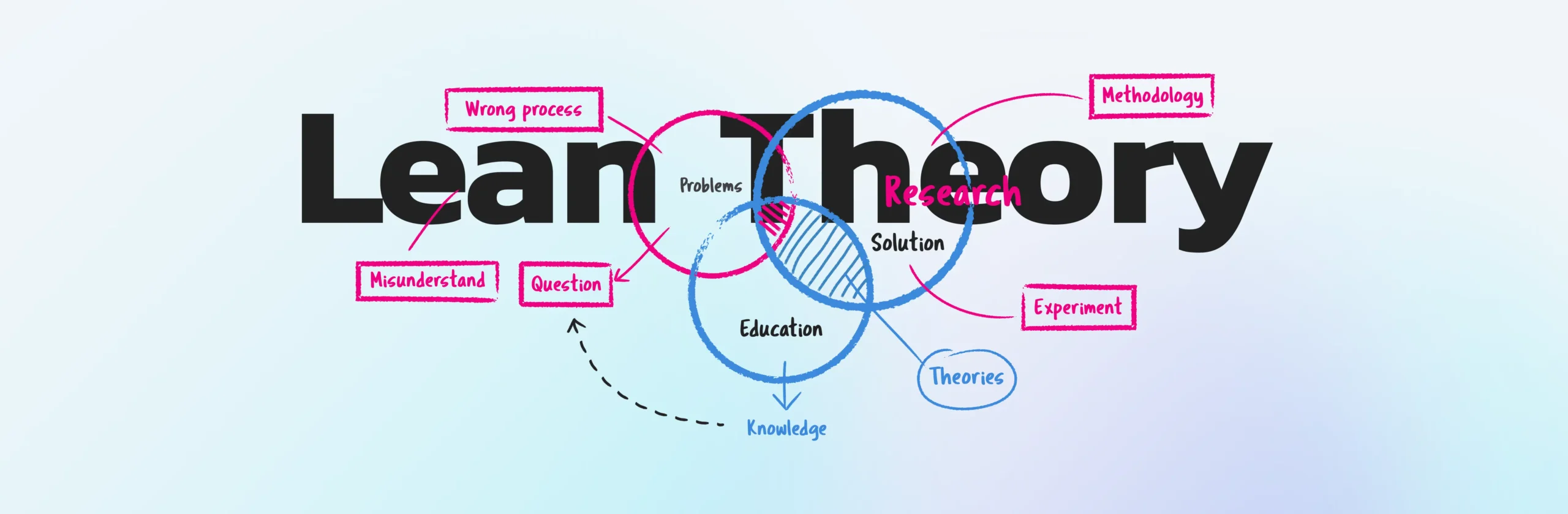
Personally, I had heard of Agile, but Lean was slightly less well-known in technology circles. After a brief search, I found that Lean revolutionized the Japanese industrial economy after World War II. This methodology was originally developed as part of the Toyota Production System. The goal was to create a production system more efficient than the mass production methods of that time.
Lean is a systematic method for eliminating waste and maximizing the flow of value through a system. Value in this definition can be defined as something your customer will pay for, because we can spend a lot of effort achieving goals that our customers don’t care about and which don’t contribute to our organization’s profitability. Value stream mapping is used by Lean in order to create a diagram that will display just where value is generated within your system and how it is flowing into your organization. Just the inverse of value is waste, i.e., effort spent on any other thing than value creation. Lean identifies three major types of wastes—all given Japanese names: muda, muri, and mura. Muda (無駄) means waste and includes any activities that don’t add value, such as overproduction, waiting, or making defects. Muri (無理) refers to overburden, where people or systems are pushed too hard, causing stress and potential failures. Finally, mura (斑) signifies unevenness, resulting in inconsistency in processes that breeds inefficiency.
While Lean began in the manufacturing world, its benefits were quickly adopted in other areas, the first being product management. Toyota was using Lean techniques in product development even as they were implementing them in manufacturing. Meeting customer demand for more variation was as important as maintaining an efficient production line for Toyota’s success.
Lean product development is characterized by:
- Independent teams of experts integrated from multiple disciplines.
- Teams empowered to manage their own work using visual work management tools.
This combination has been found to increase the rate of innovation and new product development. Lean is also inspired by statistical process control, with its focus on continuous improvement (Kaizen (改善): continuous improvement through small, ongoing changes that enhance efficiency and quality), and designed experimentation. Finally, respect for and empowerment of both the individual employee and the team is a critical part of Lean. Work can only be improved by harnessing the knowledge of those performing it.
"Lean is fundamentally about respect—respect for the customer, respect for the employee, and respect for the process." — Art Byrne
From the above, it sounds more like a team of front-end and back-end developers, operations engineers, and project managers pulling from a backlog and using a Kanban board in the typical DevOps organization. Right? That is because Lean practices are integrated within methodologies such as Agile and DevOps, which in themselves provide a way to translate Lean principles into software development whereby teams would do away with waste, continuously learn, and deliver values (Book: Lean Software Development: An Agile Toolkit).